Industrialized Construction
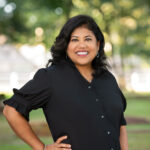
By Nushin Huq
8 min read
A Shot in the Arm for Affordable Housing?
As construction costs continue to increase, exacerbated due to COVID-related supply chain issues and inflation, manufactured housing is an increasingly attractive option for affordable housing developers. While market disruptions, such as price increases and labor shortages, have affected the manufactured housing sector as well, companies in this space are still able to construct homes at a lower cost than on-site construction.
Manufactured construction, often called industrialized construction within the industry, refers to anything from small kits-of-parts, or panels, to full volumetric modules, all of which are constructed in a factory and shipped to the construction site. Interest in homes built either modularly or with other industrialized construction methods, such as panelization, is growing due to continuous increases with onsite building costs, says Carol Galante, professor of Affordable Housing and Urban Policy at UC Berkeley College of Environmental Design.
“Generally, I think you’re seeing more and more interest in homes that are manufactured modularly or other different industrialized construction methods,” Galante says. “Just because the cost of building on-site keeps getting higher and higher, creating more demand. That said, I think progress has been slower than all that demand and pressure might indicate.”
There are different theories as to why industrialized construction hasn’t become more common place in the affordable housing space, including preconceived impressions, financing mismatch in the tax credit and modular construction worlds, as well as business challenges due to the COVID-19 pandemic. Despite challenges, a number of affordable housing veterans have embraced different forms of industrialized construction.
Embracing Industrialized Construction
Jeff Carroll, president of Tartan Residential, has been in the affordable housing space since the late 1990s. About ten years ago, Carroll conducted an experiment at one of his projects. He broke it into two phases, both with allocated tax credits, he says. One side was built with on-site construction, and the other side used industrialized construction. Otherwise, both phases were the same.
“I tallied up everything I could learn from what we were doing and walked away basically demonstrating that factory-built housing in an affordable housing tax credit-finance-world makes a lot of sense,” Carroll says.
Charlotte-based Tartan Residential builds industrialized workforce and affordable housing using structural insulated panels. The panels are slightly more expensive but are cheaper to ship than entire modules. For one of Tartan’s projects, panels were shipped thousands of miles from the factory, making a price difference in shipping significant.
Four years ago, Rick Holliday founded Vallejo, CA-based Factory_OS, which makes modular multifamily homes for affordable housing. Holliday has been working in affordable housing since the late 60s. The conventional building processes have hit costs that people just don’t believe are possible, Holliday, who is currently chief operating officer at Factory_OS, says. He gives an example of a project in Northern California that was supposed to be $700,000 a unit but ended up being $950,000 a unit.
“One of my interests before I sort of concluded my career was to see if I could take a different means and method to build housing, to save time, money and get better quality, and that’s really what Factory_OS is about,” Holliday says.
With the latest technology, industrialized construction can also offer projects a level of customization people don’t often associate with modular housing.
“The perception of prefabrication has generally been influenced by mobile homes, manufactured homes and FEMA trailers,” Holliday says. “There’s a huge difference between perception and what’s possible now.”
Factory_OS has a partnership with architecture/construction software company, Autodesk, through which they can model an entire project and add a greater level of exterior customization than most people think is possible, Holliday says.
It forces customers to change their habits, Holliday says. Design decisions are all made up front instead of along the way.
“If you’re going to order a unit from a modular manufacturer, you’ve got to go in and decide, this is the flooring, these are the cabinets, these are the fixtures,” Holliday says. “Basically, you order everything up front, and some people don’t like that, but the good news is you don’t have a bunch of change orders.”
It’s not uncommon, for example, for a project estimated initially at $10 million to end up costing $12 million due to change orders along the way, Holliday says. Modular projects don’t have change orders.
Tartan’s Carrol is keen on looking at monetizing energy efficiency in his projects. Industrial projects built with panels have to have better than twice an insulation rating, or R-value, compared to a stick frame construction, cutting heating and cooling costs by 60 to 70 percent, Carroll says. Not only does it allow them to install a smaller A/C unit, but lower utilities mean owners can charge more for rent.
Looking ahead, Carroll believes that the cost savings and value in increasing technologies in modular, panelized construction and energy efficient structures will result in more developers to either reach further down into the affordability strata – maybe hitting some incomes that they were unable to reach before or keep rents lower than they were able to before.
“We think that over the next ten years, you’re going to see more and more people move to this sort of building system. A more energy efficient structurally insulated panel, offsite factory-built type of system,” Carroll says. “We think there’s a lot of benefit there.”
Supply Chain Issues, Labor Shortages and Inflation
Even with efficiencies and automation, COVID-related supply chain issues, labor shortages and inflation haven’t left the industrialized construction industry untouched. Companies have had to adjust their business plans, but company representatives say they are still able to cope with the challenging landscape better than their on-site counterparts.
At Charlotte-based Prescient, which is a light gauge steel panel company, the challenge came in early 2021, when steel prices hit all-time highs, says Chris Coonan, director of Business Development, Western & Midwest Regions. At its peak, the steel price was close to $2,000/ton.
“Looking to the future, the steel market looks to be stabilizing below $1,000/ton,” Coonan says. “In 2022, the multifamily housing market continues to expand in strength due to the shortages of apartments in key areas of the country, as well as a peaking single-family market, which is likely excluding new buyers.”
There is some expectation for a recession in 2023 according to macro economists, Coonan says, but it will affect single-family homes more than the multifamily market.
“While the overall market may shrink, we are finding that our technology can give us the edge in highly competitive situations, and that developers and general contractors are looking for new methods and materials to deliver their projects,” Coonan says.
Throughout the pandemic, supply chain issues were problematic, but those supply chain issues are minimizing, and logistics improving, Coonan says.
The Ongoing Effects of COVID
Factory_OS has spent half its lifespan in the middle of a pandemic, which has been challenging, Holliday says. For example, supply chain issues meant windows weren’t delivered and the cost of lumber skyrocketed. Staffing was also a problem.
The entire construction industry, both the onsite and manufactured, faced workforce constraints as employees missed work due to COVID-related absences. This included absences due to illness, exposure to COVID or taking time off to care for family, Galante says.
“The absenteeism was really high,” Galante says. “Now, I think we’re over that hump.”
At Factory_OS, management implemented a vaccine mandate to combat workforce strains due to COVID, says Rick Holliday its co-founder and chief operating officer.
“We were 40 percent vaccinated this summer with a huge amount of absenteeism,” says Holliday. “We had to impose really strict vaccination requirements. We’re up to 98 percent, almost 99 percent.”
The offsite construction industry, in some ways, did better on supply chain issues than onsite construction. They place orders for their materials earlier, and they have more volume than typical onsite construction development. That said, because of inflation, the cost has definitely gone up, Galante says.
At Factory_OS, they’ve had to raise prices on their work because material prices have gone up, but their costs are still considerably less expensive than conventional buildings, Holliday says.
“You have to pay the same price for a two-by-four if you build a site-built home as I do, but I have a more efficient way to build the apartment and far less waste of material,” Holliday says. “So, we’re impacted, but I think we’re less impacted than conventional builders.”
The company had to adapt its business to account for the uncertainty in the post-COVID world.
“We’ve had to work to get agreements with suppliers to buy the materials up front and basically secure and lock down pricing,” Holliday says.
That often requires bigger deposits from customers, Holliday says. In some cases, public agencies or companies that are trying to contribute to help affordable housing will provide a deposit to a nonprofit so that they can secure their materials.
While public finance sources are sensitive to the costs of things and stretching the public subsidy, there’s still a huge disconnect in how individual affordable housing projects are financed that don’t “mesh” well with how funding is needed in a manufactured situation, Galante says.
“I think there’s a lot of work still to be done by policy to try to catch up with how you optimize the benefit of manufactured housing,” Galante says.