Housing Delivered in a Box
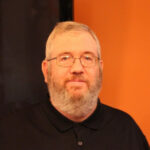
By Mark Fogarty
4 min read
Can offsite bring private tax credit financing?
Offsite construction is generating a lot of buzz on how it can transform affordable and workforce housing. But some are dreaming even bigger. Could OS create a totally private tax credit market, without the need for public money?
That’s the theory Jeffrey Carroll, principal of Tartan Residential, is putting forth. He thinks offsite construction, particularly his niche of 2D (flat) paneling, could save 20 percent of hard construction costs and eliminate the need for public gap financing familiar to all developers.
Private equity is what he has in mind for gap financing. And Carroll has a private firm, Community Development Trust of New York, an affordable housing real estate investment trust (REIT), that he says wants to be an equity investor.
Tartan, based in Charlotte, NC, thinks 2D or “flat” paneling (think of your IKEA furniture coming to you in a flat box and then needing to be assembled) represents a big savings, not just through OS in general being cheaper, but also because the cost to ship 2D is so much less than shipping completed assemblies.
Carroll plans to finance projects with tax-exempt bonds and four percent tax credits using income averaging to allow units in the workforce range, and the savings he is seeing has him musing about a completely private market in the next ten years. He is currently working on projects in Kansas City, MO and Charlotte, NC.
Consultant Douglas Koch, principal of Advisory Associates, Boston, who is involved with Carroll through the Workforce Housing Development Corp., outlined the basics of 2D panelization at the recent Summer Institute hosted by the National Housing & Rehabilitation Association in Newport, RI.
“We’ve been looking to build a better mousetrap in affordable housing for quite a while,” says Koch. He likes the idea of going with private equity, repeatable and transferrable to any part of the country where rents are high enough and costs are low enough.
“With private equity we don’t have to go tin cup in hand, we don’t have to ask for soft funds.”
Koch says that one of Carroll’s Kansas City developments, Buchanan’s Crossing, provided an accurate side-by-side savings comparison of the two methods because one phase was stick-built and another done with 2D panels.
On shipping, 2D panels cost him $250 per unit per thousand miles, far below the cost of shipping 3D. In addition to the shipping savings, “Offsite construction of highly energy efficient panels is the backbone of this whole thing,” says Carroll. The panels are highly insulated R-26 models.
Carroll has started Multifamily Buildings System, a joint venture of Tartan and manufacturer Eco-Panels, Mocksville, NC, to provide the 2D insulated panels for multifamily projects. His background is in both manufactured and affordable housing.
“After the manufactured downturn of 1999 it occurred to me that in the affordable housing world, everything is stick-built, except roofs and trusses. I was curious as to why?”
Side-by-side comparisons of stick-built and 2D 1,000 square foot units with 80 feet of exterior walls based on ones at Buchanan’s Crossing showed Carroll the panels are pricey, adding $4,200 in costs. But savings in energy efficiency, installation costs and HVAC costs came to $11,100, a net savings of $6,900 per unit.
In addition, he can foresee another $7,300 in savings per unit being achieved, for a total of $14,400. This would be coming from multi-story applications (the higher the building, the more savings), panel standardization, economies of scale and centralized purchase of windows, doors, water heaters, HVAC equipment and other items.
Carroll’s sweet spot is projects with around 120 units, with 80/60/40 income averaging, $180,000/unit total development cost, $70,000/unit tax credit equity, and $80,000/unit permanent debt, leaving a $30,000/unit funding gap.
He feels the typical public gap financing of these projects can be closed through a $10,000/unit deferred developer/general contractor fee, a $7,000/unit cost savings associated with panelization and a $13,000/unit funding gap to be filled by private equity.
Carroll believes that his efforts in workforce housing will provide substantial amounts of new construction for those who can’t afford market rates but have too much income to qualify for affordable housing. These folks currently are stuck in older “B/C class” rentals, he says.
According to Carroll, “Our objective is to establish a comprehensive platform to deliver newly-constructed apartment units for this overlooked market segment. Our goal is to produce up to 1,000 units per year, ten deals a year, in select areas within three years with continued growth thereafter.
“This is the perfect vehicle for workforce housing units, which are sorely needed.”