Rising Costs of Construction Materials
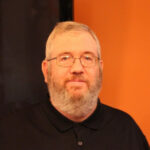
By Mark Fogarty
7 min read
A Perfect Storm for Lumber Prices
A troubling spike in lumber prices may not break until later this year, as a badly out-of-whack supply and demand equation continues to roil the construction industry.
“It was a perfect storm,” says Omar Black, vice president of preconstruction at Harkins Builders, Columbia, MD – and he’s not just speaking metaphorically.
Adding to already-pronounced industry woes set in motion by the COVID-19 pandemic last year, the storm that battered Texas in February, paralyzing the state’s electrical grid, also disrupted chemical manufacturers vital to the process.
“It was worse than some of the hurricanes that have come through there,” Black explains. “Some of the resins used to make plywood and oriented strand board (OSB) weren’t available because those factories shut down.”
A lot of demand and not enough supply was the ultimate cause of the boom in prices after the pandemic disruption, Black says.
“When COVID hit, everybody had to make some decisions about where they were going. I think some of the lumber producers were guessing demand would go down. It didn’t happen in the market I’m in, the multifamily market. Demand continued. Plus, everybody was building an outdoor deck or something to put on a restaurant or bar so they would have outdoor seating.”
There were also disruptions caused in producing companies by the rapid spread of the disease, he said.
“I’ve got to imagine sawmills and chemical providers had some instances where their production was hampered by people getting sick with COVID,” he adds. “They were probably operating at a lower level or not a full capacity depending on what did or didn’t hit in their factory or manufacturing plant.”
The result for the industry? “We have had projects shelved, and projects under construction have stopped until prices come back down.”
When will that happen? Black said prices may remain volatile this spring and summer. “There might be something that causes it to dip a little here and there,” he notes, but manufacturers are telling him “things probably won’t get better until September at the earliest. I think demand will stay this high the rest of the year. It won’t go back to Spring of 2020 levels.”
“That’s a good question,” he replies when asked if prices might spike even higher. “I think it’s just like any market. The pressures will push until the pressure can’t be borne anymore. Things have been slipping. Once I see projects starting to stop, that’s when I think prices come back down, when that pressure goes the other way.”
There’s a possibility for prices to even keep on rising, he posits, but at some point that would drive the industry towards adoption of other building materials like light gauge metal framing or structural steel.
“We’re not at that threshold yet but we’re approaching it,” he states.
John B. Cruz III, principal at the Cruz Cos. and Cruz Development Corp., Roxbury, MA, also says he thought the spike “is not going to end soon. Maybe not until the fall.”
His company saw a $700,000 boost in lumber costs on a 55-unit multifamily project. “That’s astronomical,” he states. “That puts a contractor in a pickle.”
Cruz went on, “We’ve got the resources to plow ahead and finish the building,” but says he was glad he didn’t have other projects in the pipeline suffering such a pinch.
“I hope the government gets the message and does something now,” he notes.
Enlisting the Biden Administration
In fact, the home building industry has been alarmed enough by the spike in prices to ask the Biden administration for help.
In a letter to Commerce Secretary Gina Raimondo, more than 30 organizations, including the National Association of Home Builders and the National Housing & Rehabilitation Association, note the price of lumber has almost tripled since last year and OSB is up 250 percent, with a shortage of lumber causing delivery delays.
“We respectfully request that your office examine the lumber supply chain, identify the causes for high prices and supply constraints, and seek immediate remedies that will increase production,” the letter reads.
It states that increased lumber prices added $9,000 to the cost of building an average multifamily unit, and $24,000 to an average single-family home. And it points out that lumber and OSB are essential to the remodeling and do-it-yourself sectors, as well as home construction.
“Current prices represent an intolerable and frequently insurmountable financial burden to home builders and contractors,” the trade groups write. The letter notes that the Random Lengths Framing Composite Price broke the $1,000 mark per thousand board feet for the first time ever on February 23.
The trades also reminded Congress of the beneficial economic impact construction has. “Building 1,000 average single-family homes creates 2,900 full-time jobs and generates $110.96 million in taxes and fees for all levels of government. Similarly, building 1,000 average rental apartments generates 1,250 jobs and $55.91 million in taxes and revenue,” the letter claims.
Asked if he expected any legislative or regulatory relief to come from the appeal, Harkins’ Black replies, “Anything’s possible, isn’t it?” but then added “I don’t know if that’s possible.”
Rises in lumber prices of all kinds were starkly underlined in a presentation Alex Strong, federal legislative director of the NAHB, recently gave to the Maryland Building Industry Association.
Rising Tide Lifts All Prices
All building materials prices have gone up eight percent since January 2020, he told the state group, but lumber prices hit an all-time high, with the trend line pointing straight up.
The Random Lengths Composite, which broke $1,000, started 2020 at less than $400 per thousand board feet, his figures showed.
Canadian Spruce, Pine and Fir (SPF) 2×4 prices climbed 93 percent since the fall of 2020, while Southern Yellow Pine (SYP) more than doubled to 111 percent.
Lumber futures dropped in February, Strong tells the meeting, but he says futures are not the best leading indicator.
All forms of structural panels are up more than 100 percent year over year, he said: Structural Panel Composite, up 165.8 percent; OSB Composite, up 186.1 percent; Southern Pine Plywood Composite, up 124.9 percent, and Western Fir Pine Composite, up 107.1 percent.
Steel prices rose by double digits as well, he says.
NAHB surveyed its members on pandemic-related housing challenges for home building, Strong tells the meeting, and found that a whopping 96 percent replied “yes” to seeing major or minor delays and shortages in obtaining building materials.
Second in builder challenges, at 78 percent, was local jurisdictions having trouble processing approvals, while the bronze medal, just behind at 76 percent, went to difficulty in finding workers and subcontractors willing to report to work sites.
Asking for Change
Advocacy efforts to counteract these negative trends, Strong says, will include:
- Educational meetings with new government officials;
- Letters like the one sent to Raimondo;
- Possible action to come via an Executive Order on America’s supply chains;
- Lumber webinars for state and local officials;
- Commissioning a third party to study the drivers of prices and volatility;
- Research on the impact of prices; and
- Working with multiple state attorneys general.
Another potential outcome if prices remain sky high for an extended period of time is a switch to alternate building products, like light gauge steel metal framing, although if markets return to some semblance of normality in a reasonable timeframe, that may not gain traction.
Still, some firms have made progress establishing steel framing as a viable product and that might gain more traction if there is an extended period of high lumber prices.
One thing is for sure, Harkins’ Black points out, and that’s that builders are going to have to be agile in this new environment.
“In general, this last year has been a year of trying to figure out new ways to achieve results with the barriers we have encountered,” he says.
“The guys who’ve been agile and nimble are the ones that have been able to maneuver through this more smoothly.”
Story Contacts:
Omar Black, Vice President of Preconstruction, Harkins Builders, Columbia, MD, oblack@harkinsbuilders.com
John B. Cruz III, Principal, the Cruz Companies, Roxbury, MA, jbcruz3@cruzcompanies.com
“The Housing Economy, Lumber Market, and Advocacy Efforts,” presentation to the Maryland Builders Industry Association, March 22, 2021